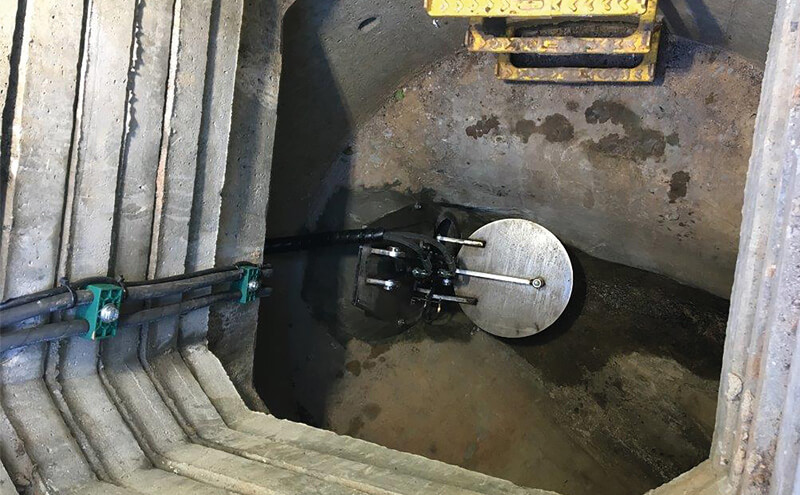
With the potential for huge fines in the event of a mishap, spill prevention is an aspect of the environmental manager’s remit where uncertainty seems no longer tolerable.
Traditional Methods of Spill Prevention
Traditional lines of defence, such as spill kits (“an essential part of any spill response plan” says the expert interviewed here) to penstocks – are unquestionably useful, but tend to rely on human or manual intervention, so fall short of guaranteed prevention.
The Shift Towards Intelligent Closure Devices
Balancing the consequences with the upfront cost of installing a prevention system is prompting many to consider the use of intelligent closure devices, whereby any points of escape to the drainage system are automatically shut off when a spill is detected. Envirotec spoke to Kirk Meikle of Aquasentry, who believes many will be unaware of the technology’s present-day affordability and ease of installation.
Relevance Across Industries
Spills can arise for all kinds of reasons, and spill prevention is an undertaking that seems relevant to every kind of business. COMAH sites and sites that store hazardous or combustible materials will obviously present the most exacting requirements. But even a spillage of something like milk or orange juice, if it finds its way into a river, can be ruinous nowadays.
Case Studies in Spill Prevention
Darcy Spillcare has provided spill prevention for retail warehouses, airports, distilleries, food manufacturers to name a few – Meikle’s customer examples draw from a fascinatingly diverse spread.
The Importance of Changing Perspectives
It’s a problem his firm has built a reputation on solving. While the methods seem well established, and not especially reliant on whizz-bang or new technology, he suggests there are changes occurring in the thought process that underpins appraising a site’s risk and advising on a solution. In the past, there seems to have been more of an ‘inward’ orientation to the problem, a preoccupation with bunded areas, spill kits and so on (still essential to ensure environmental compliance and control of spills, says Meikle). Now, the emphasis seems to be on identifying the ‘outfalls’ of a site, and working backwards, gaining a watertight awareness of where liquid material might make its way to the outside world. Increasingly, the guiding logic is “let’s find a guaranteed way of not polluting the local environment”, he says. And if this is the aim, “the only way to truly provide this guarantee is to put closure devices on.”
The Functionality of Closure Devices
These closure devices, or valves, are available in a range of sizes, from fairly small to surprisingly huge (1m diameter in the case of a part deployed by the firm at an airport), and can be deployed in varying numbers, depending on the site’s requirements.
Manual vs. Automated Solutions
In the most basic system, these might be operated manually – the ‘big red button’ approach – but Meikle advises firms to go for the automated solution, for complete peace of mind – and also for health and safety reasons. He offers the example of a factory fire: Staff will have a clearly designated fire point at which to gather, and if the valve is located elsewhere, you wouldn’t want an operator abandoning his post to locate this valve and try to close it.
Real-World Failures of Manual Intervention
Examples abound from his recent experience, where the manual intervention approach failed to prevent a damaging spill. A train maintenance depot in the South West of England had a catastrophic failure of a tank storing diesel, which found its way to the drainage system and went on to pollute the local environment. The use of an automated closure device would have avoided this.
Comparing Penstocks and Closure Devices
Penstocks are a conventional line of defence against spills, but these are mostly manually operated, unlike the closure devices from Darcy which can be automated. With penstocks, a manual operator will have to get to it in time, to be able to shut it, and the penstock might also be badly maintained or difficult to close. Also, penstocks can be expensive given their requirement for civil engineering work.
Cost-Effectiveness of Automated Systems
Closure devices can be offered either as a hydraulic or pneumatic operated system and present an opportunity for automation – whereby they will close in seconds in response to a prompt that might come from a sensor or an email. These parts are also easily retrofitted into existing drainage systems, says Meikle, which helpfully contains the cost (since there is minimal labour needed). Following closure, in the event of a spill, a waste management contractor can be called in to dispose of the collected liquid material. Job done, it seems.
Investment in Advanced Solutions
Meikle says solutions based on closure devices vary in cost and sophistication, from the simplest – the big red button approach – whereby installation of closure devices begins at around £5k, up to systems incorporating a lot of IT and intelligence. He cites a recent £40k installation at the site of a UK food manufacturer. In the latter case, the sensors and closure devices could be connected to a web portal, with operators able to access data stored in the cloud, such as historical data and the status of different parts of the system. Other add-ons might include solar panels, where it is difficult to access a power supply. The systems have the ability to self-check and notify the user if the system has a fault or when it opens and closes. And this can give the user piece of mind.
Choosing the Right Sensors
The specification also addresses the choice of sensors, appropriate to the material to be detected. Turbidity sensors might be chosen for a site storing large quantities of milk. A pH monitor is very versatile and can determine the presence of a wide range of materials, he said.
Applications of Automated Closure Systems
The deployment of these automated closure systems is normally aimed at pollution prevention or firewater runoff collection – Meikle says the split is about fifty-fifty, in the reasons why people specify this equipment. And it tends to be medium to large-size firms who opt for an automated solution, where firms are working on 14001 or 18001 compliance, or looking to work with or improve upon best practices. Prevention of reputational damage is often a big motivator.
Adhering to Best Practices
These systems can be specified in accordance with the best practice guidelines Managing Fire Water and Major Spillages, from the EA and SEPA. With fines now potentially matching company profits, in some especially severe cases brought by the EA, best practice is becoming the only option, and the logic of “if I spend £10k upfront then I don’t have to worry about this anymore”, is increasingly difficult to question. “We advise clients on best practice,” he says, “and as long as you’ve got open drainage systems, you are
vulnerable.”
Table of Contents
- Traditional Methods of Spill Prevention
- The Shift Towards Intelligent Closure Devices
- Relevance Across Industries
- Case Studies in Spill Prevention
- The Importance of Changing Perspectives
- The Functionality of Closure Devices
- Manual vs. Automated Solutions
- Real-World Failures of Manual Intervention
- Comparing Penstocks and Closure Devices
- Cost-Effectiveness of Automated Systems
- Investment in Advanced Solutions
- Choosing the Right Sensors
- Applications of Automated Closure Systems
- Adhering to Best Practices
Sign up for the latest news and offers