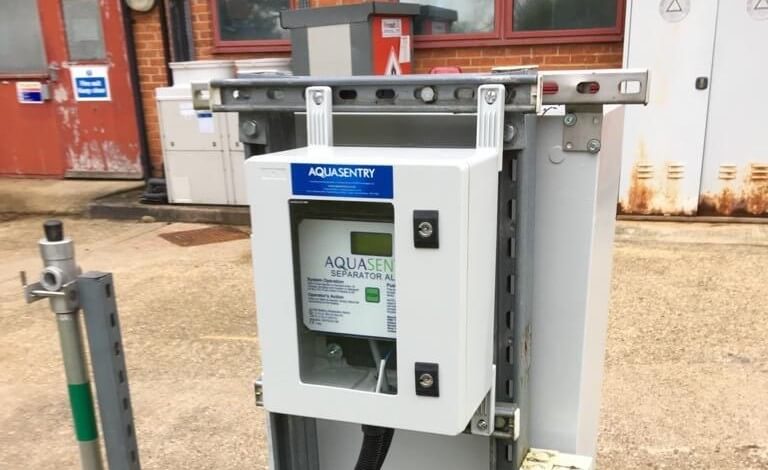
For the ostriches out there, happy to have their heads in the sand, the phrase ‘what you don’t know, won’t hurt you’ can bring a reassuring sense of comfort.
For the majority of us, however, it achieves quite the opposite effect. Given that we have more information available to us today than ever before, we would rather be safe in the knowledge that we are dealing with a full set of facts and seeing the complete picture.
In the case of site managers, tasked with ensuring pollutants don’t escape into the ground course or local waterways, information is undoubtedly a valuable currency. Being armed with up-to-the-minute data and insights into the changing status of the surrounding environment provides the means to react quickly when adverse situations arise or, ideally, prevent them from happening in the first place.
The Safeguard of Separators
As part of any site’s approach to pollution prevention, separators play a key role in safeguarding against unwanted hydrocarbons being washed into the drainage system. It is not realistic to remove all presence of diesel, petrol and oil from a site, but separators ensure they are safely contained underground and do not unwittingly find their way into nearby rivers and streams. However, the successful operation of separators depends on one important caveat: they must function correctly.
While this might sound obvious, because they are out of sight, there is a danger that separators at some sites are not given the attention they require. At other sites, there is the bigger risk that they are literally out of mind, with staff simply unaware of their presence because they were installed at a long-forgotten point in the site’s history.
In these scenarios, important question marks hang over the condition and maintenance requirements of the separator. The levels of hydrocarbons at the top of the separator will be unknown, as will the levels of silt that collect at the bottom. Without removal, the performance of the separator will be impaired, introducing the risk that oil could escape via the water outlet pipe. Any such escape may in turn lead to serious financial penalties and reputational damage.
Automated Monitoring
By adopting best practice measures, these risks are greatly reduced. For new installations, that starts with a separator that fully conforms to the Environment Agency’s European standard BSEN-858-1-2. However, it is the addition of a separator alarm that makes the biggest difference in ensuring the separator maintains optimal performance on an ongoing basis.
Separator alarm systems are comprised of a control panel and three probe sensors, each of which is installed within the separator to monitor levels of either water, oil, silt or all three. When the sensor identifies that a specified threshold level has been breached, the alarm activates automatically to notify the operations team that corrective action is required to safely remove the unwanted waste and return levels to the normal range. Alarms can be either specified as part of a new installation or retrofitted, and they are mains, battery or solar powered depending on the particular use case.
Gaining Efficiency, Saving Cost
While the primary benefit of an alarm is the knowledge that the separator is functioning as required and preventing hydrocarbon pollutants from escaping the site, there is a significant associated benefit: efficiency. Rather than committing to separator waste being extracted at regular ‘milk round’ intervals, the alarm can be relied upon to indicate when levels have been exceeded, meaning action is only taken when necessary. This also reduces the levels of intervention by site staff, reducing demands on internal resources.
Sustaining operational efficiency on an ongoing basis depends on the implementation of expert maintenance at regular intervals. This ‘MOT schedule’ assures site management that separators are operating as expected while enabling any necessary remedial work to be carried out before issues escalate into more significant problems.
In Summary
Ignorance may be bliss for some, but since we are living in the information age, there is no excuse not to take advantage of smart technologies to keep on top of potentially fast-changing situations. Separators may be out of sight, but with a separator alarm, facilities managers have ‘visibility’ of their status and peace of mind they are operating as expected.
Sign up for the latest news and offers